Fault Diagnosis, Prognosis, and Reliability for Electrical Machines and Drives
Wiley - IEEE
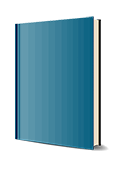
1. Auflage Oktober 2021
448 Seiten, Hardcover
Wiley & Sons Ltd
Fault Diagnosis, Prognosis, and Reliability for Electrical Machines and Drives
An insightful treatment of present and emerging technologies in fault diagnosis and failure prognosis
In Fault Diagnosis, Prognosis, and Reliability for Electrical Machines and Drives, a team of distinguished researchers delivers a comprehensive exploration of current and emerging approaches to fault diagnosis and failure prognosis of electrical machines and drives. The authors begin with foundational background, describing the physics of failure, the motor and drive designs and components that affect failure and signals, signal processing, and analysis.
The book then moves on to describe the features of these signals and the methods commonly used to extract these features to diagnose the health of a motor or drive, as well as the methods used to identify the state of health and differentiate between possible faults or their severity.
Fault Diagnosis, Prognosis, and Reliability for Electrical Machines and Drives discusses the tools used to recognize trends towards failure and the estimation of remaining useful life. It addresses the relationships between fault diagnosis, failure prognosis, and fault mitigation.
The book also provides:
* A thorough introduction to the modes of failure, how early failure precursors manifest themselves in signals, and how features extracted from these signals are processed
* A comprehensive exploration of the fault diagnosis, the results of characterization, and how they used to predict the time of failure and the confidence interval associated with it
* A focus on medium-sized drives, including induction, permanent magnet AC, reluctance, and new machine and drive types
Perfect for researchers and students who wish to study or practice in the rea of electrical machines and drives, Fault Diagnosis, Prognosis, and Reliability for Electrical Machines and Drives is also an indispensable resource for researchers with a background in signal processing or statistics.
Acknowledgments xv
Acronyms xvii
Introduction xxi
1 Basic Methods and Tools 1
1.1 General Approach 1
1.2 Feature Extraction: Signal and Preconditioning 2
1.2.1 Raw Signals: What Kind of Signals and Sensors? 2
1.2.1.1 Current Sensors 3
1.2.1.2 Vibration Measurement and Accelerometers 13
1.2.1.3 Temperature Sensors 14
1.2.1.4 Field Sensors 16
1.2.1.5 Acoustic Sensors 16
1.2.1.6 Other Sensors 18
1.2.2 Preconditioning 22
1.2.2.1 Signal Features in the Time Domain 22
1.2.2.2 Symmetric Component, Park Component 22
1.2.2.3 Symmetric Component, Park Component 24
1.2.2.4 Signal Features in the Frequency Domain 26
1.2.2.5 Wavelet Analysis 34
1.2.2.6 Instantaneous Amplitude and Frequency 35
1.2.2.7 Bilinear Time-frequency Distributions or Quadratic
Time-frequency Distributions: Cohen's Class 36
1.2.2.7.a Uncertainty Principle of Heisenberg 37
1.2.2.7.b General Representation 37
1.2.2.7.c Properties 38
1.2.2.7.d Different Representations 39
1.2.2.8 Statistic Features 45
1.2.2.9 Cyclostationarity 46
1.2.3 Model Approach 48
1.2.3.1 Kalman Observer 51
1.2.3.2 Extended Observer 52
1.2.3.3 Unscented Kalman Filter 55
1.2.4 Parity Space 56
1.3 Feature Reduction, Principal Component Analysis 60
1.3.1 Principal Component Analysis: A Space Reduction and an Unsupervised Classification 60
1.3.2 Intercorrelation 62
1.3.2.1 Pearson Coefficient "r" 62
1.3.2.2 Spearman Coefficient "rho" 63
1.3.3 Information Content: Shannon Entropy 65
1.3.4 Pattern Sizing Reduction for a Supervised Classification 65
1.3.4.1 Selection Criteria 65
1.3.4.2 Sequential Backward Feature Selection and Sequential Forward Feature Selection 67
1.3.5 Pattern Sizing Reduction for an Unsupervised Classification: Laplacian Score 68
1.3.6 Choice of the Number of Classes for an Unsupervised Classification 69
1.3.6.1 Choice of the Number of Classes with a PCA 69
1.3.6.2 General Case 70
1.3.7 Other Quality Criteria of a Classification 71
1.3.7.1 R²index 71
1.3.7.2 Calinski-Harabasz Index 72
1.3.7.3 Davies-Bouldin Index 73
1.3.7.4 Silhouette Index 73
1.3.7.5 Dunn Index 74
1.4 Classification Methods 74
1.4.1 Generalities 74
1.4.1.1 Supervised and Unsupervised Clustering 75
1.4.1.2 Measuring the Similarity: Different Distances 76
1.4.2 Supervised Clustering 77
1.4.2.1 k Nearest Neighbors 78
1.4.2.2 Support Vector Machine 80
1.4.2.3 Recurrent Neural Network 82
1.4.3 Unsupervised Clustering 85
1.4.3.1 Hierarchical Classification 86
1.4.3.2 K-means and Centroid Clustering 89
1.4.3.3 Self-organizing Map 90
1.5 Prognosis Methods 93
1.5.1 Prognosis Process 93
1.5.2 Time Series Extrapolation Methods 95
1.5.3 Bayesian Inference 101
1.5.4 Markov Chain 103
1.5.5 Hidden Markov Models 105
1.5.6 Rainflow 110
1.5.6.1 Hidden Semi-Markov Models 114
References 114
2 Applications and Specifics 125
2.1 General Presentation of Motor Drives 125
2.2 Electrical Machines 126
2.2.1 Basics 128
2.2.2 Magnetic Steel and Magnets 129
2.2.3 Windings and Insulation 133
2.3 Machine Models, Operation, and Control 137
2.3.1 Three-phase Windings 137
2.3.2 Induction Machines 138
2.3.2.1 Induction Machine Rotor Field Orientation 140
2.3.2.2 Direct Torque Control 141
2.3.3 Permanent Magnet AC Machines 144
2.4 Faults in Electrical Machines 146
2.4.1 Operational Variables and Measurements 147
2.4.2 Supervision, Detection, and Fault Classification 149
2.4.3 Bearings 153
2.4.4 Insulation 169
2.5 Open and Short Faults, Eccentricity, Broken Magnets and Rotor Bars 180
2.5.1 Induction Machines 182
2.5.1.1 Stator Fault Diagnosis 183
2.5.1.2 Eccentricity 191
2.5.1.3 Multi-fault Diagnosis with Stray Flux and Flux Sensor 193
2.5.1.4 Open Faults in Windings and Inverter 195
2.5.1.5 Broken Rotor Bars 196
2.5.2 Permanent Magnet AC Machines 198
2.5.2.1 Demagnetization of Permanent Magnets 198
2.5.2.2 Open and Short Circuit 201
2.5.3 Sensor Faults 208
2.5.4 Fault Mitigation and Management 209
2.6 Power Electronics and Systems 215
2.6.1 A Brief Description of Power Electronics in AC drives 216
2.6.2 A Brief Description of Static Switches 223
2.6.2.1 MOSFET 223
2.6.2.2 IGBT 230
2.6.2.3 Si and SiC Technology 236
2.6.2.4 Thermal Behavior 236
2.6.3 A Brief Description of Capacitors 241
2.6.3.1 General Description 241
2.6.3.2 Different Kinds of Capacitors 245
2.6.3.2.a Non-polarized Capacitors 245
2.6.3.2.b Polarized Capacitors 251
2.6.4 Device Faults and Their Manifestation 255
2.6.4.1 Basic Notion 257
2.6.4.2 On Chip Failures 258
2.6.4.3 Packaging and Chip Environment Failures 259
2.6.5 Capacitor Failure Modes 261
2.6.5.1 Failure by Degradation 261
2.6.5.2 Catastrophic Failure 262
2.6.6 Diagnosis and Prognosis Techniques for Power Devices 262
2.6.6.1 Introduction 262
2.6.6.2 Failure Modes Indicators and TSEP for Power Electronic Devices 262
2.6.6.3 Diagnosis of Failure Modes 269
2.6.6.3.a Diagnosis based on the Direct Analysis of the Current 271
2.6.6.3.b Diagnosis based on the Direct or Indirect Analysis of Junction Temperature 279
2.6.6.3.c Diagnosis based on Signal Processing 284
2.6.6.3.d Diagnosis based on Clustering 288
2.6.6.3.e Diagnosis based on Neural Network 291
2.6.6.3.f Synthesis 295
2.6.6.4 Prognosis of Failure Modes 295
2.6.6.4.a Prognosis based on Failure Mechanism and Statistical Data 295
2.6.6.4.b Prognosis based on Failure Precursors 300
2.6.7 Diagnosis and Prognosis Techniques for Capacitors 310
2.6.7.1 Fault Diagnosis Techniques 310
2.6.7.2 Methods for Predicting Electrolytic Capacitor Failures 318
Bibliography 324
3 Fault Diagnosis and Prognosis for Reliability Enhancement 345
3.1 Introduction 345
3.2 Fundamentals 346
3.2.1 The Pattern of Failures with Time for Non-Repairable Items 350
3.2.2 Distribution Functions 350
3.2.3 Confidence in Reliability and Prognosis 353
3.3 Component Reliability 354
3.4 Reliability of Subsystems and Systems 361
3.4.1 Analysis Tools 361
3.5 Lifetime, Reliability Prediction 365
3.6 Fault Management and Mitigation 368
3.7 Design and Manufacturing 371
3.8 Applications and Case Studies 372
3.9 Scheduled Maintenance, Condition-Based Maintenance 397
3.9.1 Reliability and Costs 407
3.10 Conclusions 409
Bibliography 410
Index 415
Guy Clerc is a Professor at the Université de Lyon, Ampère, in Villeurbanne, France.
Hubert Razik is a Professor at the Université de Lyon, Ampère, in Villeurbanne, France.
Abdenour Soualhi is an Assistant Professor at the LASPI Laboratory in Jean Monnet University Roanne.