Electrical Connectors
Design, Manufacture, Test, and Selection
Wiley - IEEE
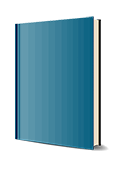
1. Auflage Januar 2021
384 Seiten, Hardcover
Wiley & Sons Ltd
Discover the foundations and nuances of electrical connectors in this comprehensive and insightful resource
Electrical Connectors: Design, Manufacture, Test, and Selection delivers a comprehensive discussion of electrical connectors, from the components and materials that comprise them to their classifications and underwater, power, and high-speed signal applications. Accomplished engineer and author Michael G. Pecht offers readers a thorough explanation of the key performance and reliability concerns and trade-offs involved in electrical connector selection.
Readers, both at introductory and advanced levels, will discover the latest industry standards for performance, reliability, and safety assurance. The book discusses everything a student or practicing engineer might require to design, manufacture, or select a connector for any targeted application. The science of contact physics, contact finishes, housing materials, and the full connector assembly process are all discussed at length, as are test methods, performance, and guidelines for various applications.
Electrical Connectors covers a wide variety of other relevant and current topics, like:
* A comprehensive description of all electrical connectors, including their materials, components, applications, and classifications
* A discussion of the design and manufacture of all parts of a connector
* Application-specific criteria for contact resistance, signal quality, and temperature rise
* An examination of key suppliers, materials used, and the different types of data provided
* A presentation of guidelines for end-users involved in connector selection and design
Perfect for connector manufacturers who select, design, and assemble connectors for their products or the end users who concern themselves with operational reliability of the system in which they're installed, Electrical Connectors also belongs on the bookshelves of students learning the basics of electrical contacts and those who seek a general reference with best-practice advice on how to choose and test connectors for targeted applications.
List of Contributors xv
Preface xvii
1 What Is an Electrical Connector? 1
Michael G. Pecht and San Kyeong
1.1 Challenges of Separable Connectors 1
1.2 Components of a Connector 2
1.2.1 Contact Springs 2
1.2.2 Contact Finishes 3
1.2.2.1 Noble Metal Contact Finishes 4
1.2.2.2 Non-noble Metal Contact Finishes 4
1.2.3 Connector Housing 4
1.2.4 Contact Interface 5
1.3 Connector Types 6
1.3.1 Board-to-Board Connectors 7
1.3.2 Wire/Cable-to-Wire/Cable Connectors 8
1.3.3 Wire/Cable-to-Board Connectors 10
1.4 Connector Terminology 11
References 14
2 Connector Housing 17
Michael G. Pecht
2.1 Mechanical Properties 17
2.2 Electrical Properties 19
2.3 Flammability 21
2.4 Temperature Rating 22
2.5 Housing Materials 23
2.5.1 Thermoplastic Polymers 25
2.5.1.1 Polyesters 25
2.5.1.2 Polyimides, Polyamide-imides, and Polyetherimides 26
2.5.1.3 Polyphenylene Sulfides 26
2.5.1.4 Polyether Ether Ketones 26
2.5.1.5 Liquid-Crystalline Polymers 27
2.5.1.6 Comparison ofThermoplastic Polymers 27
2.5.2 Thermosetting Polymers 27
2.5.3 Additives to Housing Materials 29
2.5.4 Manufacturing of Housing Materials 29
References 30
3 Contact Spring 31
Michael G. Pecht
3.1 Copper Alloys 31
3.1.1 Unified Number System (UNS) 31
3.1.2 Properties of Copper Alloys 33
3.2 Nickel Alloys 37
3.3 Conductive Elastomers 37
3.4 Contact Manufacturing 38
References 41
4 Contact Plating 43
Michael G. Pecht
4.1 Noble Metal Plating 43
4.1.1 Gold 44
4.1.2 Palladium 46
4.1.3 Combination of Gold and Palladium 47
4.2 Non-noble Metal Plating 47
4.2.1 Silver 48
4.2.1.1 Characteristics of Silver as a Contact Finish 49
4.2.1.2 Potential Tarnish-Accelerating Factors 50
4.2.1.3 Use of Silver in Typical Connectors 53
4.2.1.4 Managing Silver Corrosion 54
4.2.2 Silver-Palladium Alloys 55
4.2.3 Nanocrystalline Silver Alloys 55
4.2.4 Silver-Bismuth Alloys 57
4.2.5 Tin 57
4.2.6 Nickel Contact Finishes 59
4.3 Underplating 59
4.4 Plating Process 60
4.4.1 Electrolytic Plating 61
4.4.1.1 Rack Plating 61
4.4.1.2 Barrel Plating 61
4.4.2 Electroless Plating 62
4.4.3 Cladding 63
4.4.4 Hot Dipping 63
References 63
5 Insertion and Extraction Forces 67
Michael G. Pecht
5.1 Insertion and Extraction Forces 67
5.2 Contact Retention 70
5.3 Contact Force and Deflection 70
5.4 Contact Wipe 71
References 73
6 Contact Interface 75
Michael G. Pecht and San Kyeong
6.1 Constriction Resistance 76
6.2 Contact Resistance 77
6.3 Other Factors Affecting Contact Resistance 79
6.4 Current Rating 81
6.5 Capacitance and Inductance 82
6.6 Bandpass and Bandwidth 86
References 87
7 The Back-End Connection 89
Chien-Ming Huang, San Kyeong and Michael G. Pecht
7.1 Soldered Connection 89
7.2 Press-Fit Connection 93
7.3 Crimping Connection 95
7.4 Insulation Displacement Connection 98
References 98
8 Loads and Failure Mechanisms 103
San Kyeong, Lovlesh Kaushik and Michael G. Pecht
8.1 Environmental Loads 104
8.1.1 Temperature 104
8.1.2 Vibration Load 105
8.1.3 Humidity 106
8.1.4 Contamination 107
8.1.5 Differential Pressure 108
8.2 Failure Mechanisms in Electrical Connectors 109
8.2.1 Silver Migration 110
8.2.2 Tin Whiskers 114
8.2.3 Corrosion Failure 119
8.2.3.1 Dry Corrosion 119
8.2.3.2 Galvanic Corrosion 120
8.2.3.3 Pore Corrosion 121
8.2.3.4 Creep Corrosion 121
8.2.3.5 Fretting Corrosion 123
8.2.4 Arc Formation 124
8.2.5 Creep Failure 128
8.2.6 Wear 131
8.2.6.1 Adhesive Wear 132
8.2.6.2 Abrasive Wear 133
8.2.6.3 Fatigue Wear 134
8.2.6.4 Corrosive Wear 134
8.2.6.5 Fretting Wear 135
8.2.7 Frictional Polymerization 136
8.3 Case Study by NASA: Electrical Connectors for Spacecraft 137
References 139
9 Fretting in Connectors 147
Deepak Bondre and Michael G. Pecht
9.1 Mechanisms of Fretting Failure 149
9.1.1 Material Factors That Affect Fretting 152
9.1.1.1 Contact Materials 152
9.1.1.2 Hardness 155
9.1.1.3 Surface Finish 155
9.1.1.4 Frictional Polymerization 156
9.1.1.5 Grain Size 156
9.1.1.6 Oxides 157
9.1.1.7 Coefficient of Friction 158
9.1.1.8 Electrochemical Factor 158
9.1.2 Operating Factors That Affect Fretting 158
9.1.2.1 Contact Load 158
9.1.2.2 Fretting Frequency 159
9.1.2.3 Slip Amplitude 162
9.1.2.4 Electric Current 162
9.1.3 Environmental Factors That Affect Fretting 163
9.1.3.1 Humidity 164
9.1.3.2 Temperature 164
9.1.3.3 Dust 165
9.2 Reducing the Damage of Fretting 167
9.2.1 Lubrication 168
9.2.2 Improvement in Design 168
9.2.3 Coatings 169
References 170
10 Testing 173
Bhanu Sood andMichael G. Pecht
10.1 Dielectric With standing Voltage Testing 173
10.2 Insulation Resistance Testing 174
10.3 Contact Resistance Testing 176
10.4 Current Rating 179
10.5 Electromagnetic Interference and Electromagnetic Compatibility Testing 180
10.6 Temperature Life Testing 181
10.7 Thermal Cycling Testing 182
10.8 Thermal Shock Testing 182
10.9 Steady-State Humidity Testing 183
10.10 Temperature Cycling with Humidity Testing 184
10.11 Corrosion 184
10.11.1 Dry Corrosion 185
10.11.2 Creep Corrosion 186
10.11.3 Moist Corrosion 187
10.11.4 Fretting Corrosion 187
10.12 Mixed Flowing Gas Testing 188
10.12.1 Battelle Labs MFG Test Methods 189
10.12.2 EIA MFG Test Methods: EIA 364-TP65A 190
10.12.3 IEC MFG Test Methods: IEC 68-2-60 Part 2 190
10.12.4 Telcordia MFG Test Methods: Telcordia GR-63-CORE Section 5.5 191
10.12.5 IBM MFG Test Methods: G1(T) 191
10.12.6 CALCE MFG Chamber Capability 192
10.13 Vibration 192
10.13.1 Mechanical Shock 193
10.13.2 Mating Durability 193
10.14 Highly Accelerated Life Testing 194
10.15 Environmental Stress Screening 194
References 195
11 Supplier Selection 197
Michael H. Azarian, Diganta Das and Michael G. Pecht
11.1 Connector Reliability 197
11.2 Capability Maturity Models 198
11.3 Key Reliability Practices 198
11.3.1 Reliability Requirements and Planning 199
11.3.2 Training and Development 200
11.3.3 Reliability Analysis 200
11.3.4 Reliability Testing 201
11.3.5 Supply-Chain Management 201
11.3.6 Failure Data Tracking and Analysis 202
11.3.7 Verification and Validation 202
11.3.8 Reliability Improvement 203
11.4 Reliability Capability of an Organization 203
11.5 The Evaluation Process 204
References 205
12 Selecting the Right Connector 207
Ilknur Baylakoglu and San Kyeong
12.1 Connector Requirements Based on Design and Targeted Application 207
12.2 Mating Cycles 208
12.3 Current and Power Ratings 209
12.4 Environmental Conditions 212
12.5 Termination Types 213
12.6 Materials 213
12.6.1 Connector Housing Materials 216
12.6.2 Connector Spring Materials 217
12.7 Contact Finishes 217
12.8 Reliability 218
12.9 Raw Cables and Assemblies 219
12.10 Supplier Reliability Capability Maturity 219
12.11 Connector Selection Team 220
12.12 Selection of Candidate Parts from a Preferred Parts Database 221
12.13 Electronic Product Manufacturers' Parts Databases 221
12.14 Parts Procurement 223
12.15 Parts Availability 223
12.16 High-Speed Connector Selection 224
12.17 NASA Connector Selection 224
12.18 Harsh Environment Connector Selection 227
12.19 Fiber-Optic Interconnect Requirements by Market 229
12.20 High-Power Subsea Connector Selection 229
12.20.1 Undersea Connector Reliability 231
12.21 Screening Tests 232
12.22 Low-Voltage Automotive Single- and Multiple-Pole Connector Validation 236
12.23 Failure Modes, Mechanisms, and Effects Analysis for Connectors 236
12.24 Connector Experiments 242
12.25 Summary 246
References 246
13 Signal Connector Selection 251
Michael G. Pecht
13.1 Issues Involving High-Speed Connectors 251
13.2 Signal Transmission Quality Considerations 252
13.2.1 Interconnect Delays 252
13.2.2 Signal Distortion 252
13.3 Electromagnetic Compatibility 253
13.4 Virtual Prototyping 254
13.4.1 TDR Impedance Measurements 255
13.4.1.1 Reflection Coefficient 255
13.4.1.2 TDR Resolution Factors 256
13.4.1.3 TDR Accuracy Factors 257
13.5 Vector Network Analyzer 259
13.6 Simulation Program with Integrated Circuit Emphasis (SPICE) 259
References 260
14 Advanced Technology Attachment Connectors 261
Neda Shafiei, Kyle LoGiudice and Michael G. Pecht
14.1 ATA Connector and SATA Connector Overview 261
14.2 History of ATA and SATA 263
14.3 Physical Description of ATA Connectors, ATA Alternative Connectors, and SATA Connectors 264
14.4 ATA Standardization and Revisions 268
14.5 SATA Standardization and Revisions 270
14.6 SATA in the Future 272
References 273
15 Power Connectors 275
Michael G. Pecht and San Kyeong
15.1 Requirements for Power Connectors 275
15.2 Power Connector Materials 276
15.3 Types of Power Connectors 277
15.4 Power Contact Resistance 280
15.5 Continuous, Transient, and Overload Current Capacities 282
15.5.1 Continuous Current Capacity 282
15.5.2 Transient Current Capacity 283
15.5.3 Overload Current Capacity 284
15.6 Current Rating Method 284
References 286
16 Electrical Connectors for Underwater Applications 289
Flore Remouit, Jens Engström and Pablo Ruiz-Minguela
16.1 Background and Terminology 290
16.1.1 History 291
16.1.2 Terminology 291
16.2 Commercial Off-the-Shelf (COTS) Connectors 292
16.2.1 Rubber-Molded 292
16.2.2 Rigid-Shell or Bulkhead Assemblies 293
16.2.3 Fluid-Filled UnderwaterMateable 294
16.2.4 Inductive Coupling 295
16.2.5 Assemblies (Non-unmateable) 295
16.3 Connector Design 296
16.3.1 Thermal Design 296
16.3.2 Electrical Properties 297
16.3.3 Mechanical Properties 299
16.3.4 Material Choices 300
16.3.5 Specifications for Underwater Connectors 301
16.4 Connector Deployment and Operation 302
16.4.1 Connection Procedure 302
16.4.2 Connection Layout 303
16.4.3 Reliability 305
16.5 Discussion and Conclusion 305
References 306
17 Examples of Connectors 313
Lei Su, Xiaonan Yu, San Kyeong andMichael G. Pecht
17.1 Amphenol ICC M-Series(TM) 56 Connectors 313
17.2 Amphenol ICC Paladin(r)Connectors 313
17.3 Amphenol ICC 3000W EnergyEdge(TM) X-treme Card Edge Series 314
17.4 Amphenol ICC FLTStack Connectors 314
17.5 Amphenol ICC HSBridge Connector System 315
17.6 Amphenol ICC MUSBR Series USB 3.0 Type-A Connectors 315
17.7 Amphenol ICCWaterproof USB Type-C(TM) Connectors 316
17.8 Amphenol ICC NETBridge(TM) Connectors 316
17.9 Amphenol Sine Systems DuraMate(TM) AHDP Circular Connectors 317
17.10 Amphenol Aerospace MIL-DTL-38999 Series III Connectors 318
17.11 Fischer Connectors UltiMate(TM) Series Connectors 318
17.12 Hirose Electric DF50 Series Connectors 319
17.13 Hirose Electric microSD(TM) Card Connectors 320
17.14 Molex SAS-3 and U.2 (SFF-8639) Backplane Connectors 320
17.15 Molex NeoPress(TM) Mezzanine Connectors 321
17.16 Molex Impel(TM) Plus Backplane Connectors 321
17.17 Molex EXTreme Guardian(TM) Power Connectors 322
17.18 Molex Imperium(TM) High Voltage/High Current Connectors 323
17.19 TE Connectivity Free Height Connectors 323
17.20 TE Connectivity STRADAWhisper Connectors 323
17.21 TE ConnectivityMULTI-BEAM High-Density (HD) Connectors 324
17.22 TE Connectivity HDMI(TM) Connectors 325
17.23 TE Connectivity AMP CT Connector Series 325
17.24 TE ConnectivityMicro Motor Connectors 326
17.25 TE Connectivity AMPSEAL Connectors 326
17.26 TE Connectivity M12 X-Code Connectors 327
17.27 TE Connectivity SOLARLOK 2.0 Connectors 327
17.28 TE Connectivity Busbar Connectors 328
References 329
Appendix
Standards 331
A.1 Standard References for Quality Management and Assurance 332
A.2 General Specifications for Connectors 332
A.3 Safety-Related Standards and Specifications 332
A.4 Standard References for Connector Manufacturing 333
A.5 Standard References for Socket Material Property Characterization 334
A.6 Standard References for Socket Performance Qualification 335
A.7 Standard References for Socket Reliability Qualification 336
A.8 Other Standards and Specifications 338
A.9 Telcordia 338
A.10 Society of Cable Telecommunications Engineers (SCTE) 339
A.11 Electronic Industries Alliance/Telecommunications Industry Association (EIA/TIA) 339
A.12 International Electrotechnical Commission (IEC) 340
A.12.1 IEC Standards 341
A.12.2 IEC Connectors 341
A.13 Military Standards (MIL-STD) 341
A.14 Standards for Space-Grade Connectors 342
References 345
Index 347
MICHAEL G. PECHT, PHD, is Chair Professor and Director of the Center for Advanced Life Cycle Engineering (CALCE) at the University of Maryland, USA. He received his PhD in Engineering Mechanics from the University of Wisconsin at Madison, USA. He is an IEEE, ASME, SAE, and IMAPS Fellow.