Sustainable Development in the Process Industries
Cases and Impact
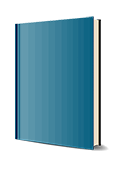
1. Edition April 2010
288 Pages, Hardcover
Practical Approach Book
Short Description
Because of the growing interest among petroleum, recycling, and other industries, sustainability is central to chemical engineers and students. Sustainable Development in the Process Industry not only explores but also demonstrates practical solutions for using sustainable technologies, focusing on three major points: people, prosperity, and planet. Rather than presenting theories, the text provides examples and cases studies ranging from the petroleum industry to the water processing industry. With a collection of international authors, the text is suitable for any chemical engineer or student interested in achieving a more sustainable world.
The complete, hands-on guide to sustainable development
Today's process industries must develop natural resources within an eco-friendly framework that balances current demand with future need. Realizing this goal necessitates global vigilance of three key areas-people, planet, and prosperity-known as the Triple Bottom Line or, simply, the Triple P.
Sustainable Development in the Process Industries details how worldwide implementation of sustainable processes in present-day industries can positively influence the Triple P going forward by lowering poverty, reducing pollution, and conserving resources. This in-depth guide includes:
* Real-world case studies and examples
* Individual chapters written by industry experts
* Application in industries such as petroleum and fuel, food, recycling, mineral processing, and water processing
* Focus on the micro (molecules, unit operations, processes) to the macro (industrial sites, value chains, regions, the world)
Providing lessons with practical application rather than pure theory, Sustainable Development in the Process Industries offers sound solutions to social, ecological, and economic challenges imperative to assuring our planet's well-being for generations.
1.1. Reason for this book.
1.2. Scope of the book.
1.3. Use in education.
1.4. Use in industry.
2 Sustainability Metrics, Indicators, and Indices for the Process Industries.
2.1 Overview and scope.
2.2 Hierarchy of SD Metrics, Indices, and Indicators.
2.3 Practical tools for the Process Industries.
2.4 Summary and Conclusions.
2.5 References.
3 Resource Efficiency of Chemical Manufacturing Chains - Present and Future.
3.1 Introduction.
3.2 Resource Efficiency.
3.3 Economic Impact.
3.4 Conclusions.
3.5 List of Symbols.
3.6 Notation.
3.7 References.
4 Regional integration of processes, agriculture and society.
4.1 The formative character of raw materials.
4.2 The systemic engineering challenge.
4.3 Regional integration of technologies.
4.4 Dedication.
4.5 Literature.
5 Eco-Industrial Parks in the Netherlands: the Rotterdam Harbour and Industry Complex.
5.1 Introduction.
5.2 Industrial Ecosystem Programmes in Rotterdam.
5.3 Conclusions.
5.4 References.
6 By-product Synergy Networks: Driving Innovation through Waste Reduction and Carbon Mitigation.
6.1 Introduction to By-product synergy (BPS).
6.2 BPS origins.
6.3 By-product Synergy, the Process.
6.4 Barriers and Challenges.
6.5 Benefits and Opportunities.
6.6 Examples.
6.7 Conclusion.
6.8 References.
7 Fast pyrolysis of biomass for energy and chemicals: Technologies at pilot plant, demo-plant and commercial scale.
7.1 Introduction.
7.2 Oil properties.
7.3 Fast Pyrolysis Process technologies.
7.4 Mass and energy balance for production of bio-oil and char in a 2 t/hr wood plant.
7.5 Bio-oil fuel Applications.
7.6 Chemicals from bio-oil.
7.7 Economics.
7.8 Concluding remarks.
7.9 Nomenclature.
7.10 References.
8 The Integrated Corn-Based Biorefinery: A Case Study in Sustainable Process Development.
8.1 Introduction.
8.2 Technology Development for an Integrated Corn-Based Biorefinery.
8.3 LCA Results: ICBR versus Benchmarks.
8.4 Final reflections.
Acknowledgements.
References.
9. Cellulosic Biofuels - a sustainable option for Transportation.
9.1. Introduction.
9.2. Case studies.
9.3. Sustainability of cellulosic biofuels.
9.4. Conclusions and Recommendations for R&D Activities.
9.5. References.
10 DSM's New Integrated Urea-Melamine Process: A Sustainable Industrial Process Development.
10.1 Introduction.
10.2 Urea Production.
10.3 Conventional DSM Stamicarbon Gas-Phase Melamine Production Process.
10.4 New Integrated Urea-Melamine Process.
10.5 Conclusions.
10.6 References.
11 Sustainable Innovation in the Chemical Industry: An overview of commercial impacts.
11.1 Overview.
11.2 Historical Perspective.
11.3 Innovations in the Age of Sustainability.
11.4 Sustainability driven by innovation and performance.
11.5 Acknowledgements.
11.6 Notation.
11.7 References.
12 Implementation of sustainable strategies in Small-Medium Enterprises (SME's) based upon the concept of Cleaner Production: A case study from an anodizing company.
12.1 Overview.
12.2 Sustainable management needs active strategies.
12.3 Eloxieranstalt A. Heuberger GmbH - sustainable management in an anodizing plant.
12.4 Conclusions.
12.5 Acknowledgements.
12.6 Appendix.
12.7 The author.
12.8 References.
13 Microbial Engineering and Bioleaching: Application to the Sustainable Concepts of Metals Recycling and Mineral Processing.
13.1 Overview.
13.2 Bioleaching Process Design and Development.
13.3 How to design a Bioleaching reactor: Applicability of the Core particle model?
13.4 Industrial applications.
13.5 Conclusion.
13.6 References.
14 Application of Industrial Ecosystem Principles in Industrial Symbiosis (By-Product Synergy) - Successful Experience from The Dow Chemical Company.
14.1 Introduction.
14.2 Relationship between Industrial Symbiosis (By-Product Synergy) and Sustainable Development.
14.3 Challenges, Barriers and Counter Measures in Exploration, Evaluation and Implementation of Industrial Symbiosis (By-Product Synergy).
14.4 What Is By-Product Synergy and What Is Not?
14.5 Work Process and Successful Cases of Industrial Symbiosis (By-Product Synergy).
14.6 Conclusions and Recommendations.
14.7 Acknowledgement.
14.8 References.
Joseph B. Powell is Shell's Chief Scientist, Chemical Engineering. He joined the Process Development Department at Shell's Westhollow Technology Center (Houston) in 1988, where he has led major R&D programs. Dr. Powell has been granted forty-five U.S. patents and several industry awards, including the A. D. Little Award for Chemical Engineering Innovation (AIChE 1998).